FIBERS
Introduction
Fibers are often investigated in forensic science as they are a form of evidence that obeys Locard’s Exchange principle,that is, every contact leaves a trace. When dealing with fibers coming from an unknown source (for example, fibers found on a body), it is the examiner’s task to first identify these fibers, and then to compare them with a sample of known provinance (for example, fibers from the suspect’s garment). Textile fibers occur as a multitude of different types. The forensic examination of fibers requires the scientist to have a thorough knowledge of and experience in the area of fiber technology and classification. The aim of this article is to present and discuss the most common types of fibers likely to be encountered in forensic examinations.
Classification of Fibers
A commonly accepted classification begins by dividing fibers into two groups: natural and manmade (artifical)fibers.
The natural fibers may then be subdivided into three classes: animal (protein), vegetable (cellulose) and mineral (asbestos). Animal fibers are further subdivided into three groups, depending on the protein composition and/or utilization: silk (fibroin), wool (keratin)and hair fibers (also keratin). The vegetable fibers are also subdivided into three groups, depending on which part of the plant is the source of the fiber: seed fibers, bast (stem) fibers and leaf fibers. The naturally occurring mineral fibers are asbestos.
Artificial fibers are subdivided into three groups: synthetic-polymer fibers, natural-polymer fibers and other fibers.
The natural fibers may then be subdivided into three classes: animal (protein), vegetable (cellulose) and mineral (asbestos). Animal fibers are further subdivided into three groups, depending on the protein composition and/or utilization: silk (fibroin), wool (keratin)and hair fibers (also keratin). The vegetable fibers are also subdivided into three groups, depending on which part of the plant is the source of the fiber: seed fibers, bast (stem) fibers and leaf fibers. The naturally occurring mineral fibers are asbestos.
Artificial fibers are subdivided into three groups: synthetic-polymer fibers, natural-polymer fibers and other fibers.
Natural Fibers Animal fibers
All animal fibers are protein based. The difference between proteins arises from different functional groups pendant to the main chain. For example, silk is composed of the protein fibroin whereas wool and other animal hairs are composed of keratin.
Silk Silk is obtained from a class of insects called Lepidoptera. Silk fiber is produced in filament form (> 1 km) by the larvae of caterpillars when the cocoons are formed. The principal species cultivated for commercial production of silk is Bombyx mori, the mulberry silkworm. Tussah silk is produced by Antherea pernyi, the wild silkworm.
In the raw state silk filaments consist of two fibers of fibroin embedded in sericin (silk gum). After commercial de-gumming Bombyx silk fibers are transparent, uniform in width (9-12 um) with smooth and structureless surfaces (they look like synthetic fibers). Tussah silk fibers are darker in color, coarser and less uniform in width (average 28 um), with pronounced longitudinal striations.
As a fiber for textile use the outstanding properties of silk are its strength, toughness, high regain, excellent soft handle, resistance to creasing, good draping properties and luxurious appearance. Its high cost has restricted its use mainly to top quality apparel goods such as ladies’ frocks, blouses, underwear, stockings, handkerchiefs and men shirts and ties.

Figure 1 Classification of fibers
An example of silk fiber is shown in Fig. 2.
Hair fibers All animal fibers except silk can be considered as hair fibers (in its wider definition). They come from many sources including: ovine (sheep, goat, etc.), camel family (camel, alpaca, vicuna, etc.), or rodent (rat). However, the term ‘wool’ is generally applied to sheep hair, whereas the simple term ‘hair’ fibers, or sometimes ‘specialty’ hair fibers, refers to other animal hairs.
Wool and hair fibers are composed of keratin, which is a protein containing a high concentration of sulfur. These fibers are linear polymers with a high ratio of disulfide bonds which help to stabilize the fiber structure. Hair fibers are resistant to acids and solvents, but are altered by basic and oxidizing solutions.
Hairs are composed of three types of cells: cuticle cells, cortical cells and medulla cells. As shown in Fig. 3, the cuticle cells form an outer sheath which encases the inner cortical cells. The cuticle scales overlap each other with the exposed edges pointing toward the tip of the fiber contributing to the tactile properties of the fiber. The number of scale layers and the degree of overlap determines the width of the cuticle. The scale pattern is a useful identification criterion. Scale pattern can vary within different basic hair types (coarse versus fine) within hairs from a single species. Scale pattern can vary in a repeatable and systematic way along the length of individual hairs.

Figure 2 Silk fiber (magnification 90 x).

Figure 3 Schematic of a wool/hair fiber.
The medulla is usually a centrally located structure, or canal, which can be continuous, discontinuous or fragmented. The structure of the medulla and the ratio between the medulla diameter and the hair diameter (MI = medullar index) are valuable features for the identification of the generic class. It should be noted that, in wool fibers, the medulla is generally present only in coarse fibers (average diameter >30 um).
The most common hair fibers are as follows:
• Wool: hair from the sheep. Wool fibers show a great variation in both their physical and chemical properties, due to the multitude of variations possible in diet, breed, health, climate, etc. For example, the length can vary from 3 to 30 cm, and the diameter from 17 to 42 um (both features are dependent on each other). Merino wool is sought after for its fineness, softness, strength, elasticity and crimp. Merino wool has superior spinning properties and is used for spinning the finest woollen and worsted yarns. Medium wools, produced by breeds such as Leicester, Cheviot, Corriedale and Polwarth are used in the manufacture of woollens, knitting yarns, hosiery, blankets, etc. An example of wool fiber is shown in Fig. 4.
• Mohair: hair from the angora goat. Mohair fibers have a length of 20-30 cm and a diameter of 1070 um. Generally these fibers have no medulla. Mohair has similar physical and chemical properties to wool.
• Cashmere: originally hair from the Asiatic goat Capra hircus laniger. Hair produced from selectively bred wild goats of Australia, New Zealand and Scotland is also called cashmere. These fibers are 5-10 cm in length with diameters of 14-16 um. Cashmere is chemically identical to wool, but because of its fineness and better wetting properties, is more susceptible to chemical damage, especially with respect to alkalis. Cashmere is higly regarded for producing garments which are comfortable and have soft handle. The main uses are in high class ladies dress goods and knitwear.
• Camel: hair from the camel or dromedary. The finer inner camel hair has found use in men’s high grade overcoating, whereas the longer outer hair is used mainly in beltings and inner linings.
• Alpaca: hair from the fleece of the alpaca (Lama pacos) which inhabits South America. Alpaca fibers have a diameter of 24-26 um, with a distinctive scale structure and medullation. They have similar uses to mohair.
• Vicuna: undercoat hair from the vicuna, the rarest and smallest of the llama family. The diameter is 13-14 um. These fibers are as valuable as cashmere and have similar uses.
• Angora: hair from the pelts of the angora rabbit. The hair is shorn from the pelts and separated by blowing. The fine hair is used to make felts for the hat trade, and the long guard hair is spun into yarn. The best hair is 6-8 cm long and about 13 umin diameter. Rabbit hair is often blended with wool or nylon.
• Others: hairs from domestic pets and farm animals (cat, dog, cow, horse, etc.) and hairs from humans (head hairs, pubic hairs, etc.) may be encountered in forensic examinations.

Figure 4 Merino woolfiber (magnification 90 x).
Silk Silk is obtained from a class of insects called Lepidoptera. Silk fiber is produced in filament form (> 1 km) by the larvae of caterpillars when the cocoons are formed. The principal species cultivated for commercial production of silk is Bombyx mori, the mulberry silkworm. Tussah silk is produced by Antherea pernyi, the wild silkworm.
In the raw state silk filaments consist of two fibers of fibroin embedded in sericin (silk gum). After commercial de-gumming Bombyx silk fibers are transparent, uniform in width (9-12 um) with smooth and structureless surfaces (they look like synthetic fibers). Tussah silk fibers are darker in color, coarser and less uniform in width (average 28 um), with pronounced longitudinal striations.
As a fiber for textile use the outstanding properties of silk are its strength, toughness, high regain, excellent soft handle, resistance to creasing, good draping properties and luxurious appearance. Its high cost has restricted its use mainly to top quality apparel goods such as ladies’ frocks, blouses, underwear, stockings, handkerchiefs and men shirts and ties.
Figure 1 Classification of fibers
An example of silk fiber is shown in Fig. 2.
Hair fibers All animal fibers except silk can be considered as hair fibers (in its wider definition). They come from many sources including: ovine (sheep, goat, etc.), camel family (camel, alpaca, vicuna, etc.), or rodent (rat). However, the term ‘wool’ is generally applied to sheep hair, whereas the simple term ‘hair’ fibers, or sometimes ‘specialty’ hair fibers, refers to other animal hairs.
Wool and hair fibers are composed of keratin, which is a protein containing a high concentration of sulfur. These fibers are linear polymers with a high ratio of disulfide bonds which help to stabilize the fiber structure. Hair fibers are resistant to acids and solvents, but are altered by basic and oxidizing solutions.
Hairs are composed of three types of cells: cuticle cells, cortical cells and medulla cells. As shown in Fig. 3, the cuticle cells form an outer sheath which encases the inner cortical cells. The cuticle scales overlap each other with the exposed edges pointing toward the tip of the fiber contributing to the tactile properties of the fiber. The number of scale layers and the degree of overlap determines the width of the cuticle. The scale pattern is a useful identification criterion. Scale pattern can vary within different basic hair types (coarse versus fine) within hairs from a single species. Scale pattern can vary in a repeatable and systematic way along the length of individual hairs.
Figure 2 Silk fiber (magnification 90 x).
Figure 3 Schematic of a wool/hair fiber.
The medulla is usually a centrally located structure, or canal, which can be continuous, discontinuous or fragmented. The structure of the medulla and the ratio between the medulla diameter and the hair diameter (MI = medullar index) are valuable features for the identification of the generic class. It should be noted that, in wool fibers, the medulla is generally present only in coarse fibers (average diameter >30 um).
The most common hair fibers are as follows:
• Wool: hair from the sheep. Wool fibers show a great variation in both their physical and chemical properties, due to the multitude of variations possible in diet, breed, health, climate, etc. For example, the length can vary from 3 to 30 cm, and the diameter from 17 to 42 um (both features are dependent on each other). Merino wool is sought after for its fineness, softness, strength, elasticity and crimp. Merino wool has superior spinning properties and is used for spinning the finest woollen and worsted yarns. Medium wools, produced by breeds such as Leicester, Cheviot, Corriedale and Polwarth are used in the manufacture of woollens, knitting yarns, hosiery, blankets, etc. An example of wool fiber is shown in Fig. 4.
• Mohair: hair from the angora goat. Mohair fibers have a length of 20-30 cm and a diameter of 1070 um. Generally these fibers have no medulla. Mohair has similar physical and chemical properties to wool.
• Cashmere: originally hair from the Asiatic goat Capra hircus laniger. Hair produced from selectively bred wild goats of Australia, New Zealand and Scotland is also called cashmere. These fibers are 5-10 cm in length with diameters of 14-16 um. Cashmere is chemically identical to wool, but because of its fineness and better wetting properties, is more susceptible to chemical damage, especially with respect to alkalis. Cashmere is higly regarded for producing garments which are comfortable and have soft handle. The main uses are in high class ladies dress goods and knitwear.
• Camel: hair from the camel or dromedary. The finer inner camel hair has found use in men’s high grade overcoating, whereas the longer outer hair is used mainly in beltings and inner linings.
• Alpaca: hair from the fleece of the alpaca (Lama pacos) which inhabits South America. Alpaca fibers have a diameter of 24-26 um, with a distinctive scale structure and medullation. They have similar uses to mohair.
• Vicuna: undercoat hair from the vicuna, the rarest and smallest of the llama family. The diameter is 13-14 um. These fibers are as valuable as cashmere and have similar uses.
• Angora: hair from the pelts of the angora rabbit. The hair is shorn from the pelts and separated by blowing. The fine hair is used to make felts for the hat trade, and the long guard hair is spun into yarn. The best hair is 6-8 cm long and about 13 umin diameter. Rabbit hair is often blended with wool or nylon.
• Others: hairs from domestic pets and farm animals (cat, dog, cow, horse, etc.) and hairs from humans (head hairs, pubic hairs, etc.) may be encountered in forensic examinations.
Figure 4 Merino woolfiber (magnification 90 x).
Vegetable fibers
The vegetable fibers are divided into three groups depending on the section of the plant from which they are harvested.
• seed fibers: cotton, kapok and coir;
• bast (stem) fibers: flax, ramie, hemp, kenaf and jute;
• leaf fibers: sisal, henequin, abaca and New Zealand hemp.
The use of the term fiber has different meanings for a botanist and a textile scientist. With vegetable fibers the botanical origin may be a true botanical fiber (bast and leaf fibers) or a seed hair (cotton). Textile vegetable fibers usually contain groups or bundles of single fibers called ultimates. The degree of coarseness of the textile fiber depends on whether or not these groups are separated by physical and/or chemical disruption.
All vegetable fibers contain the same chemical constituents including cellulose and hemicellulose,lignins, pectins, water solubles and fats and waxes. They have, however, distinguishable lengths, bundles and cell wall shapes. In addition, the composition, the general appearance and the surface quality can be modified through the manufacturing process (e.g. mercerized cotton). These fibers have generally a high tensile strength but they are easy to crease.
Cotton Cotton is a fiber attached to the seed of several species of the genus Gossypium. Originally from India, cotton is now grown in many subtropical countries. The principal species include G. barba-dense (South America and Egypt), G. hirsutum Central America, USA, 80% of the world production) and G. arboreum and G. herbaceum (Indian and Arabic countries).
Cotton is composed of approximately 92% cellulose. After maturation, as drying proceeds, the walls of the fiber shrink and collapse, the central hollow lumen becomes smaller and flatter, and the fiber develops convolution (twists). There are from 110 (fine) to 60 (coarse Asian cotton) convolutions per centimeter in cotton fibers. These convolutions improve the flexibility of the fiber and hence the spinning properties of the cotton. The convolutions are an important morphological feature used in microscopic identification of cotton.
The morphological appearance and the crystalline structure can be modified by a special procedure using sodium hydroxide (NaOH) and mechanical elongation. This process, invented by the English chemist John Mercer, in 1844, produces mercerized cotton. Mercerized cotton has greatly reduced convolutions.
Cotton fibers can be dyed with a wide range of dyestuffs including direct, azoic, vat, sulfur, reactive and metal complex dyes. Cotton fibers are resistant to solvents. However, they are damaged by strong acids, oxidizing agents and strong bases.
The mechanical properties of cotton fibers are in the middle range. The use of cotton is, therefore, very wide. As a result, cotton represents more than half of the world’s annual quantity of textile fibers. An example of cotton fiber is shown in Fig. 5.
Kapok These seed fibers are obtained from the pods of the kapok tree, Ceiba petrandra (baobab family). Kapok fibers have an average length of 18 mm and a diameter of 20-30 um. The fiber is oval in cross-section with a wide lumen and a very thin wall. Kapok fibers are composed of about 65% cellulose with the balance being mainly lignins and hemicellu-lose. Kapok fibers have a low density and are unsuitable for spinning into yarn. As a result they are principally used as a filling in such products as life-buoys, belts, mattresses and pillows. Kapok fibers were popular before World War II (over 40 million kg per annum). However, production has since dropped dramatically owing to destruction of plantations and the development of alternative fiber fillings (e.g. polyester Dacron).

Figure 5 Cotton fiber (magnification 90 x).
Coir These fibers are contained between the outer husk of the coconut and the shell of the inner kernel. Coir fibers are coarse, with a length of 15-36 cm, and diameters of 0.1-1.5 mm. The virgin coir fibers comprise about 40% cellulose, 40% lignin, 2% pectin and 18% hemicellulose. The process of retting removes much of the pectins and hemicellulose so that the commercial fibers consist essentially of cellulose and lignin. Coir has a high tensile strength which is retained after prolonged immersion in water. As a result, coir is used in the manufacture of brushes, brooms and door mats. Coir also has a good resistance to microbiological attack.
Flax Flax fibers are bast fibers from the stalk of the plant hinum usitatissimum. In the flax plant, the fibers are arranged in bundles of 12-40 fibers. These bundles are up to 100 cm in length and 15-20 umin diameter. Flax fibers are mainly polygonal in cross-section, caused by the way that they are packed together in bundles. Each ultimate fiber is pointed at both ends, and there is a small lumen running lengthwise but disappearing near the ends. The fibers have a smooth surface except at intervals where they are ringed with transverse nodes. These nodes, which are useful in identifying the fiber, help to bind the fibers together, and their regular and frequent occurrence is important for the formation of fine strong yarns. An example of flax fiber is shown in Fig. 6.
Flax fibers have a much higher content of noncellulosic material than cotton. Flax contains about 75% cellulose, 15% hemicellulose, 2.5% pectins and 2% lignins. The quality and spinning properties of flax are very dependent on the 1-1.5% wax present. This gives the fibers their high luster as well as imparting suppleness.

Figure 6 Flax fiber (magnification 90 x).
Flax fibers are stronger than other natural fibers, and are much less pliable and elastic than other common natural fibers. Flax has about the same moisture regain as cotton but absorbs moisture much more rapidly, making it very suitable for towels and drying cloths. The smooth fiber surface makes it very easy to launder, hence historically flax found great use in the manufacture of table cloths and bandages. Fine fabric woven from flax is termed linen.
Flax is more difficult to dye than cotton. However, flax bleaches to a full white which is enhanced by its natural luster. This characteristic is much prized in household linens, so only a small portion is dyed.
Ramie The commercial source of ramie fiber is Boehermeria nivea, which is grown as a perennial. The extraction of ramie is much more difficult than that of flax, jute and hemp fibers, and this difficulty has restricted its use. The ultimate ramie fibers vary in length from 2.5 to 30 cm with diameters ranging from 40 to 75 um. The cells, which are elongated in cross-section, have thick walls, with a well-defined lumen. The fiber surface is characterized by small node-like ridges and striations. The orientation of the molecules in ramie is very regular, and it is the most crystalline of the natural cellulosic fibers.
Natural ramie consists essentially of about 75% cellulose, 16% hemicellulose, 2% pectins, 1% lig-nins, and 6% water solubles and waxes. After decortification, the cellulose content rises to about 85%, and the fully de-gummed fiber contains 96-98% cellulose on a dry basis.
Ramie fibers are very white with a silk-like luster and hence make attractive fabrics. Ramie is unaffected by exposure to sunlight and has a very high resistance to bacteria, fungi and mildew. Ramie fabrics and yarns, like linen, are highly absorbent and dry quickly. Fabrics are easily laundered and show only minor strength loss after repeated washings. Durable and attractive sheets, table cloths and towels can be made from ramie.
Hemp Hemp is the bast fiber produced from the stalk of the plant Cannabis sativa. Fiber strands vary from 1.0 to 2.0 m in length with the ultimate cells in the range of 0.5-5.0 cm in length and 15-50 umin diameter. These ultimate cells are similar in appearance to flax, except that the fiber surface has longitudinal fractures (no nodes) and the cell ends are blunt and irregularly shaped.
The composition of dry hemp fibers is about 75% cellulose, 17% hemicellulose, 1% pectins, 3.6% lig-nins, 2.7% water solubles and 0.8% fats and waxes. Hemp fibers are gray-green to brown in color with the better quality fibers having a luster. Their strength, elongation, etc. are very similar to flax, and, in some instances, good quality hemp can be used as a substitute for flax. The main commercial uses of hemp are in the manufacture of ropes, cords, string and twine.
Jute Jute is the bast fiber obtained from Corchorus capsularis and C. elitorius plants. The jute fiber strands comprise bundles of spindle-shaped single cells or ultimates. These ultimates vary in length from 1 to 6 mm, with an average of 3.1 mm, being much shorter than cotton fibers. The diameter is in the range 15-25 um. They have a polygonal cross-section with a large lumen and thick cell walls. The surface of the cells is mainly smooth with only occasional markings.
The main components of raw dry jute fibers are 71% cellulose, 13% lignin, 13% hemicellulose, 0.2% pectin, 2.3% water solubles and 0.5% fats and waxes. The presence of hemicellulose makes jute more sensitive to alkalis and acids than pure cellulose. Unbleached jute is extremely light sensitive and turns yellow or brown on prolonged exposure with a loss in tensile strength. The sensitivity to light appears to be connected with the high lignin content.
Jute is fairly lustrous with moderate strength. However, it is inextensible and brittle. Jute finds application in packaging for foods, cotton, etc. as backing for linoleum and carpets, and in the manufacture of ropes and cordages.
Kenaf The fiber kenaf is obtained from the plant Hibiscus cannabinus and is similar to jute in many of its properties, hence kenaf is a substitute for jute.
Sisal Sisal fibers are obtained from the leaves of the tropical plant Agave sisalana. Individual strands of sisal have a length of 1-2 m and are white to yellowish in color. The fiber bundles consist of ultimates which are 3-7 mm in length and have an average diameter of 24 um. The fibers have a broad lumen and the fiber ends are broad and blunt and sometimes forked. The fibers are polygonal in cross-section, sometimes with rounded edges. The main use of sisal is for the manufacture of ropes, cordages, twines, etc.
• seed fibers: cotton, kapok and coir;
• bast (stem) fibers: flax, ramie, hemp, kenaf and jute;
• leaf fibers: sisal, henequin, abaca and New Zealand hemp.
The use of the term fiber has different meanings for a botanist and a textile scientist. With vegetable fibers the botanical origin may be a true botanical fiber (bast and leaf fibers) or a seed hair (cotton). Textile vegetable fibers usually contain groups or bundles of single fibers called ultimates. The degree of coarseness of the textile fiber depends on whether or not these groups are separated by physical and/or chemical disruption.
All vegetable fibers contain the same chemical constituents including cellulose and hemicellulose,lignins, pectins, water solubles and fats and waxes. They have, however, distinguishable lengths, bundles and cell wall shapes. In addition, the composition, the general appearance and the surface quality can be modified through the manufacturing process (e.g. mercerized cotton). These fibers have generally a high tensile strength but they are easy to crease.
Cotton Cotton is a fiber attached to the seed of several species of the genus Gossypium. Originally from India, cotton is now grown in many subtropical countries. The principal species include G. barba-dense (South America and Egypt), G. hirsutum Central America, USA, 80% of the world production) and G. arboreum and G. herbaceum (Indian and Arabic countries).
Cotton is composed of approximately 92% cellulose. After maturation, as drying proceeds, the walls of the fiber shrink and collapse, the central hollow lumen becomes smaller and flatter, and the fiber develops convolution (twists). There are from 110 (fine) to 60 (coarse Asian cotton) convolutions per centimeter in cotton fibers. These convolutions improve the flexibility of the fiber and hence the spinning properties of the cotton. The convolutions are an important morphological feature used in microscopic identification of cotton.
The morphological appearance and the crystalline structure can be modified by a special procedure using sodium hydroxide (NaOH) and mechanical elongation. This process, invented by the English chemist John Mercer, in 1844, produces mercerized cotton. Mercerized cotton has greatly reduced convolutions.
Cotton fibers can be dyed with a wide range of dyestuffs including direct, azoic, vat, sulfur, reactive and metal complex dyes. Cotton fibers are resistant to solvents. However, they are damaged by strong acids, oxidizing agents and strong bases.
The mechanical properties of cotton fibers are in the middle range. The use of cotton is, therefore, very wide. As a result, cotton represents more than half of the world’s annual quantity of textile fibers. An example of cotton fiber is shown in Fig. 5.
Kapok These seed fibers are obtained from the pods of the kapok tree, Ceiba petrandra (baobab family). Kapok fibers have an average length of 18 mm and a diameter of 20-30 um. The fiber is oval in cross-section with a wide lumen and a very thin wall. Kapok fibers are composed of about 65% cellulose with the balance being mainly lignins and hemicellu-lose. Kapok fibers have a low density and are unsuitable for spinning into yarn. As a result they are principally used as a filling in such products as life-buoys, belts, mattresses and pillows. Kapok fibers were popular before World War II (over 40 million kg per annum). However, production has since dropped dramatically owing to destruction of plantations and the development of alternative fiber fillings (e.g. polyester Dacron).
Figure 5 Cotton fiber (magnification 90 x).
Coir These fibers are contained between the outer husk of the coconut and the shell of the inner kernel. Coir fibers are coarse, with a length of 15-36 cm, and diameters of 0.1-1.5 mm. The virgin coir fibers comprise about 40% cellulose, 40% lignin, 2% pectin and 18% hemicellulose. The process of retting removes much of the pectins and hemicellulose so that the commercial fibers consist essentially of cellulose and lignin. Coir has a high tensile strength which is retained after prolonged immersion in water. As a result, coir is used in the manufacture of brushes, brooms and door mats. Coir also has a good resistance to microbiological attack.
Flax Flax fibers are bast fibers from the stalk of the plant hinum usitatissimum. In the flax plant, the fibers are arranged in bundles of 12-40 fibers. These bundles are up to 100 cm in length and 15-20 umin diameter. Flax fibers are mainly polygonal in cross-section, caused by the way that they are packed together in bundles. Each ultimate fiber is pointed at both ends, and there is a small lumen running lengthwise but disappearing near the ends. The fibers have a smooth surface except at intervals where they are ringed with transverse nodes. These nodes, which are useful in identifying the fiber, help to bind the fibers together, and their regular and frequent occurrence is important for the formation of fine strong yarns. An example of flax fiber is shown in Fig. 6.
Flax fibers have a much higher content of noncellulosic material than cotton. Flax contains about 75% cellulose, 15% hemicellulose, 2.5% pectins and 2% lignins. The quality and spinning properties of flax are very dependent on the 1-1.5% wax present. This gives the fibers their high luster as well as imparting suppleness.
Figure 6 Flax fiber (magnification 90 x).
Flax fibers are stronger than other natural fibers, and are much less pliable and elastic than other common natural fibers. Flax has about the same moisture regain as cotton but absorbs moisture much more rapidly, making it very suitable for towels and drying cloths. The smooth fiber surface makes it very easy to launder, hence historically flax found great use in the manufacture of table cloths and bandages. Fine fabric woven from flax is termed linen.
Flax is more difficult to dye than cotton. However, flax bleaches to a full white which is enhanced by its natural luster. This characteristic is much prized in household linens, so only a small portion is dyed.
Ramie The commercial source of ramie fiber is Boehermeria nivea, which is grown as a perennial. The extraction of ramie is much more difficult than that of flax, jute and hemp fibers, and this difficulty has restricted its use. The ultimate ramie fibers vary in length from 2.5 to 30 cm with diameters ranging from 40 to 75 um. The cells, which are elongated in cross-section, have thick walls, with a well-defined lumen. The fiber surface is characterized by small node-like ridges and striations. The orientation of the molecules in ramie is very regular, and it is the most crystalline of the natural cellulosic fibers.
Natural ramie consists essentially of about 75% cellulose, 16% hemicellulose, 2% pectins, 1% lig-nins, and 6% water solubles and waxes. After decortification, the cellulose content rises to about 85%, and the fully de-gummed fiber contains 96-98% cellulose on a dry basis.
Ramie fibers are very white with a silk-like luster and hence make attractive fabrics. Ramie is unaffected by exposure to sunlight and has a very high resistance to bacteria, fungi and mildew. Ramie fabrics and yarns, like linen, are highly absorbent and dry quickly. Fabrics are easily laundered and show only minor strength loss after repeated washings. Durable and attractive sheets, table cloths and towels can be made from ramie.
Hemp Hemp is the bast fiber produced from the stalk of the plant Cannabis sativa. Fiber strands vary from 1.0 to 2.0 m in length with the ultimate cells in the range of 0.5-5.0 cm in length and 15-50 umin diameter. These ultimate cells are similar in appearance to flax, except that the fiber surface has longitudinal fractures (no nodes) and the cell ends are blunt and irregularly shaped.
The composition of dry hemp fibers is about 75% cellulose, 17% hemicellulose, 1% pectins, 3.6% lig-nins, 2.7% water solubles and 0.8% fats and waxes. Hemp fibers are gray-green to brown in color with the better quality fibers having a luster. Their strength, elongation, etc. are very similar to flax, and, in some instances, good quality hemp can be used as a substitute for flax. The main commercial uses of hemp are in the manufacture of ropes, cords, string and twine.
Jute Jute is the bast fiber obtained from Corchorus capsularis and C. elitorius plants. The jute fiber strands comprise bundles of spindle-shaped single cells or ultimates. These ultimates vary in length from 1 to 6 mm, with an average of 3.1 mm, being much shorter than cotton fibers. The diameter is in the range 15-25 um. They have a polygonal cross-section with a large lumen and thick cell walls. The surface of the cells is mainly smooth with only occasional markings.
The main components of raw dry jute fibers are 71% cellulose, 13% lignin, 13% hemicellulose, 0.2% pectin, 2.3% water solubles and 0.5% fats and waxes. The presence of hemicellulose makes jute more sensitive to alkalis and acids than pure cellulose. Unbleached jute is extremely light sensitive and turns yellow or brown on prolonged exposure with a loss in tensile strength. The sensitivity to light appears to be connected with the high lignin content.
Jute is fairly lustrous with moderate strength. However, it is inextensible and brittle. Jute finds application in packaging for foods, cotton, etc. as backing for linoleum and carpets, and in the manufacture of ropes and cordages.
Kenaf The fiber kenaf is obtained from the plant Hibiscus cannabinus and is similar to jute in many of its properties, hence kenaf is a substitute for jute.
Sisal Sisal fibers are obtained from the leaves of the tropical plant Agave sisalana. Individual strands of sisal have a length of 1-2 m and are white to yellowish in color. The fiber bundles consist of ultimates which are 3-7 mm in length and have an average diameter of 24 um. The fibers have a broad lumen and the fiber ends are broad and blunt and sometimes forked. The fibers are polygonal in cross-section, sometimes with rounded edges. The main use of sisal is for the manufacture of ropes, cordages, twines, etc.
Henequin
Henequin is another important agave leaf fiber from the plant Agave forcroydes. Henequin is native of the Mexican state of Yucatan. The physical and chemical properties of henequin are almost identical to sisal.
Abaca (Manila hemp) Abaca is produced from the leaf of the plant Musa textilis, a member of the banana family indigenous to the Philippines. The fiber strands have a length of 1-3 m and diameter of 0.050.30 mm. The ultimate fibers are 3-12 mm in length and 16-32 um in diameter. The cross-section is irregularly round or oval in shape, and the lumen is very large and generally empty. The fiber cells have thin smooth walls and sharp or pointed ends. Abaca is used for the manufacture of better quality ropes and cordages.
New Zealand hemp (Phormium tenax) Phormium tenax, or New Zealand hemp, is a perennial plant indigenous to New Zealand. The ultimate fibers have a length of 2.5-15 mm and diameter of 10-20 um. The cells are nearly circular in cross-section with a circular lumen. The composition of leaf fibers of Phormium tenax differ from other leaf fibers in having much lower cellulose content but higher hemicel-lulose and lignin contents.
Abaca (Manila hemp) Abaca is produced from the leaf of the plant Musa textilis, a member of the banana family indigenous to the Philippines. The fiber strands have a length of 1-3 m and diameter of 0.050.30 mm. The ultimate fibers are 3-12 mm in length and 16-32 um in diameter. The cross-section is irregularly round or oval in shape, and the lumen is very large and generally empty. The fiber cells have thin smooth walls and sharp or pointed ends. Abaca is used for the manufacture of better quality ropes and cordages.
New Zealand hemp (Phormium tenax) Phormium tenax, or New Zealand hemp, is a perennial plant indigenous to New Zealand. The ultimate fibers have a length of 2.5-15 mm and diameter of 10-20 um. The cells are nearly circular in cross-section with a circular lumen. The composition of leaf fibers of Phormium tenax differ from other leaf fibers in having much lower cellulose content but higher hemicel-lulose and lignin contents.
Mineral fibers (asbestos)
The term asbestos applies to a variety of mineral fibers that have a high elasticity and a high resistance to heat, corrosion, wear and tear, humidity, etc. These fibers are noncombustible and have a weak electricity conductivity. Asbestos is easily mixed with building materials (glue, plaster, concrete, etc.). As a result, until relatively recently substantial quantities of asbestos were mined. However, health considerations have since greatly reduced the industry. Asbestos has been replaced wherever possible by other fibers such as glass or Nomex.
The different forms of asbestos vary in composition, dimension and crystalline structure (Table 1) However, all forms are silicates. The fibers are very fine (approx. 0.02 um – 2000 times finer than a human hair) and relatively long (several millimeters).
The different forms of asbestos vary in composition, dimension and crystalline structure (Table 1) However, all forms are silicates. The fibers are very fine (approx. 0.02 um – 2000 times finer than a human hair) and relatively long (several millimeters).
Table 1 Common forms of asbestos
Group | Chemical formula |
Serpentine group | |
Chrysotile (white) | Mg6Si401o(OH)8 |
Amphibole group | |
Crocidolite (blue, the most | Na2Fe32+Fe23+Si8022(OH,F)2 |
hazardous) | |
Cummingtonite-grunerite | (Mg,Fe2+)7Si8022(0H)2 |
(amosite, brown) | |
Tremolite-actinolite | Ca2(Mg,Fe2+)5Si8022(0H)2 |
Anthophyllite | (Mg,Fe2+)7Si8022(0H,F)2 |
The different forms can be identified using polarizing microscopy and transmission electron microscopy (TEM).
The most important form of asbestos is chrysotile which accounted for about 90% of total asbestos production. Chrysotile belongs to the serpentine group of minerals and occurs only in serpentine rocks. These are metamorphic rocks, and the development of chrysotile seems to depend on a hydrothermal recrystallization, which is probably initiated at cracks in the rock. The fibers grow at the expense of the adjacent rock. This form is important in a forensic context, because it is used as an ingredient in safe manufacture. When recovered on a suspect’s garment, it can therefore constitute a very specific trace evidence.
The most important form of asbestos is chrysotile which accounted for about 90% of total asbestos production. Chrysotile belongs to the serpentine group of minerals and occurs only in serpentine rocks. These are metamorphic rocks, and the development of chrysotile seems to depend on a hydrothermal recrystallization, which is probably initiated at cracks in the rock. The fibers grow at the expense of the adjacent rock. This form is important in a forensic context, because it is used as an ingredient in safe manufacture. When recovered on a suspect’s garment, it can therefore constitute a very specific trace evidence.
Artificial Fibers
Artificial fibers may be derived from natural polymers (regenerated fibers such as viscose, rayon, cellulose acetate and triacetate, etc.) or synthesized from simple starting material (synthetic fibers such as polyamides, polyesters, polyurethanes, etc.).
Whether made from a natural or synthetic starting material the aim in making an artificial fiber is to replicate natural fibers but in the process either improve on some limitations of natural fibers or produce an inexpensive alternative. The ‘improvements’ in artificial fibers often relate to the ability of textile manufacturers to produce fabrics or products with chosen characteristics and the ability to color fibers. The processes used to manufacture artificial fibers are controlled to attempt to produce fibers with defined properties especially with regard to crystallinity and orientation. These contribute to the physical properties of the fibers and the fabric produced from them. The wide range of fibers and fabrics give much greater flexibility and scope to the textile manufacturer than in the era before artificial fibers. However, the fact that cotton still represents more than 50% of textiles and products demonstrates the inability of synthetic fibers to improve on the natural properties of cotton as a textile fiber.
The basis of artificial fiber formation is the same for both regenerated and synthetic fibers. The polymer in a concentrated, viscous form, either in solution or in a molten state, is forced through the tiny holes of a spinneret, and the emerging filaments are immediately precipitated or cooled to form the solid-state fiber. This process is termed spinning or extrusion and may be accomplished in different ways. The fiber filaments thus formed are usually stretched or drawn mechanically. This operation causes the polymer chains to become more aligned (or oriented) in the direction of the longitudinal axis.
The longitudinal and cross-sectional appearance of artificial fibers is largely affected by the manufacturing process. For example, the shape of spinneret holes will determine the cross-section; the orientation of the polymer chains will influence the longitudinal appearance under polarized light, etc.
A guide to most common synthetic fibers is shown in Table 2.
Artificial fibers from natural polymers
Fibers can be regenerated from two natural sources:
• a biological source:
• cellulose: viscose, modal rayon, cuprammonium rayon, cellulose esters;
• protein: casein;
• seaweed: alginate fibers;
• a mineral source:
• glass
• metallized yarn.
Fibers regenerated from a mineral source are rather classified as ‘other artificial fibers’ because their source is not a real polymer.
The most common regenerated fibers are cellulosic. Depending on the subclass, these fibers have variable properties (mechanical properties, degree of polymerization, etc.). However, their longitudinal appearance is very similar (uniform diameter with longitudinal striations and irregular cross-section) except cupro (where the surface is smooth and the cross-section is almost round).
Viscose Viscose is the most important regenerated cellulose fiber with respect to its production level. The manufacturing process involves first the aging of cellulose pulp in alkali solution (NaOH). The cellulose pulp is then solubilized by forming the carbon disulfide derivative of cellulose known as cellulose xan-thate (cellulose-O-CSSNa). This solution is allowed to ripen to an appropriately viscous consistency, and is then extruded through a spinneret. The emerging filaments are immediately coagulated in an aqueous bath containing sulfuric acid and salts of sodium and zinc sulfate. The coagulation bath completely regenerates the xanthate derivative back into the form of cellulose. The filaments thus formed are drawn from the bath at a controlled rate with some degree of applied stretch.
Whether made from a natural or synthetic starting material the aim in making an artificial fiber is to replicate natural fibers but in the process either improve on some limitations of natural fibers or produce an inexpensive alternative. The ‘improvements’ in artificial fibers often relate to the ability of textile manufacturers to produce fabrics or products with chosen characteristics and the ability to color fibers. The processes used to manufacture artificial fibers are controlled to attempt to produce fibers with defined properties especially with regard to crystallinity and orientation. These contribute to the physical properties of the fibers and the fabric produced from them. The wide range of fibers and fabrics give much greater flexibility and scope to the textile manufacturer than in the era before artificial fibers. However, the fact that cotton still represents more than 50% of textiles and products demonstrates the inability of synthetic fibers to improve on the natural properties of cotton as a textile fiber.
The basis of artificial fiber formation is the same for both regenerated and synthetic fibers. The polymer in a concentrated, viscous form, either in solution or in a molten state, is forced through the tiny holes of a spinneret, and the emerging filaments are immediately precipitated or cooled to form the solid-state fiber. This process is termed spinning or extrusion and may be accomplished in different ways. The fiber filaments thus formed are usually stretched or drawn mechanically. This operation causes the polymer chains to become more aligned (or oriented) in the direction of the longitudinal axis.
The longitudinal and cross-sectional appearance of artificial fibers is largely affected by the manufacturing process. For example, the shape of spinneret holes will determine the cross-section; the orientation of the polymer chains will influence the longitudinal appearance under polarized light, etc.
A guide to most common synthetic fibers is shown in Table 2.
Artificial fibers from natural polymers
Fibers can be regenerated from two natural sources:
• a biological source:
• cellulose: viscose, modal rayon, cuprammonium rayon, cellulose esters;
• protein: casein;
• seaweed: alginate fibers;
• a mineral source:
• glass
• metallized yarn.
Fibers regenerated from a mineral source are rather classified as ‘other artificial fibers’ because their source is not a real polymer.
The most common regenerated fibers are cellulosic. Depending on the subclass, these fibers have variable properties (mechanical properties, degree of polymerization, etc.). However, their longitudinal appearance is very similar (uniform diameter with longitudinal striations and irregular cross-section) except cupro (where the surface is smooth and the cross-section is almost round).
Viscose Viscose is the most important regenerated cellulose fiber with respect to its production level. The manufacturing process involves first the aging of cellulose pulp in alkali solution (NaOH). The cellulose pulp is then solubilized by forming the carbon disulfide derivative of cellulose known as cellulose xan-thate (cellulose-O-CSSNa). This solution is allowed to ripen to an appropriately viscous consistency, and is then extruded through a spinneret. The emerging filaments are immediately coagulated in an aqueous bath containing sulfuric acid and salts of sodium and zinc sulfate. The coagulation bath completely regenerates the xanthate derivative back into the form of cellulose. The filaments thus formed are drawn from the bath at a controlled rate with some degree of applied stretch.
Table 2 Quick guide to artificialfibers (Courtesy American Fiber Manufacturers Association, Washington, DC)
Major generic man-made fibers | Characteristics | Major domestic and industrial uses |
Acetate | Luxurious feeland appearance | Apparel: blouses, dresses, and foundation |
Celanese, Celebrate, | Wide range of colors and lusters | garments, lingerie, linings, shirts, slacks, |
Chromspun, Estron, | Excellent drapability and softness | sportswear |
Microsafe | Relatively fast-drying | Fabrics: brocade, crepe, double knits, faille, |
Shrink-, moth-, and mildew-resistant | knitted jerseys, lace, satin, taffeta, tricot | |
Home furnishings: draperies, upholstery | ||
Other: cigarette filters, fiberfil for pillows, quited | ||
products | ||
Acrylic | Soft and warm | Apparel: dresses, infant wear, knitted garments, |
Acrilan, Acrilan Plus, Bounce- | Wool-like | ski wear, socks, sportswear, sweaters |
Back, Creslan, Cystar, | Retains shape | Fabrics: fleece and pile fabrics, face fabrics in |
Cyster AF, Duraspun | Resilient | bonded fabrics, simulated furs, jerseys |
Quick-drying | Home furnishings: blankets, carpets, draperies, | |
Resistant to moths, sunlight, oil and | upholstery | |
chemicals | Other: auto tops, awnings, hand-knitting and | |
craft yarns, industrialand geotextile fabrics | ||
Aramid | Does not melt | Hot-gas filtration fabrics, protective clothing, |
Kevlar, Nomex, Fi-lana, Pil-Trol, | Highly flame-resistant | military helmets, protective vests, structural |
Sayelle, So-Lara, Smart | High strength | composites for boats, sailcloth, tires, ropes |
Yarns, Ware-Dated, Wintuk | High resistance to stretch | and cables, mechanical rubber goods, |
Maintains its shape and form at high | marine and sporting goods | |
temperatures | ||
Lyocell | Soft, strong, absorbent | Dresses, slacks and coats |
Lenzing Lyocell, Tencel | Good dyeability | |
Filrillates during wet processing | ||
produce specialtextures | ||
Modacrylic | Soft | Apparel: deep pile coats, trims, linings, |
SEF Plus | Resilient | simulated fur, wigs and hairpieces |
Abrasion- and flame-resistant | Fabrics: fleece fabrics, industrial fabrics, knit- | |
Quick-drying | pile fabric backings, non-woven fabrics | |
Resists acids and alkalis | Home furnishings: awnings, blankets, carpets, | |
Retains shape | flame-resistant draperies and curtains, | |
scatter rugs | ||
Other: filters, paint rollers, stuffed toys | ||
Nylon | Exceptionally strong | Apparel: blouses, dresses, foundation |
A.C.E., Anso, Antron, | Supple | garments, hosiery, lingerie and underwear, |
Assurance, Avantige, | Abrasion-resistant | raincoats, ski and snow apparel, suits, |
Cantrece, Capima, Caplana, | Lustrous | windbreakers |
Caprolan,Captiva, Cordura, | Easy to wash | Home furnishings: bedspreads, carpets, |
Creme de Captiva, | Resists damage from oiland many | draperies, curtains, upholstery |
Crepeset, Durasoft, | chemicals | Other: air hoses, conveyor and seat belts, |
DyeNAMIX, Eclipse, | Resilient low in moisture absorbency | parachutes, racket strings, ropes and nets, |
Hardline, Hydrofil, Hytel, | sleeping bags, tarpaulins, tents, thread, tire | |
Matinesse, Microsupplex, | cord, geotextiles | |
No Shock, PowerSilk, | ||
Resistat, Shimmereen, Silky | ||
Touch, Solution, Sportouch, | ||
Stainmaster, Stay Gard, | ||
Supplex, Tactel, Tru- | ||
Ballistic, Ultra Image, Ultra | ||
Touch, Ultron, Wear-Dated, | ||
Wellon, Wellstrand, | ||
WorryFree, Zefsport, Zeftron |
Table 2 (continued) Quick guide to artificialfibers
Major generic man-made fibers | Characteristics | Major domestic and industrial uses |
Olefin | Unique wicking properties that make very | Apparel: pantyhose, underwear, knitted sports |
Alpha, Essera, Impressa, | comfortable | shirts, men’s half hose, men’s knitted |
Innova, Marvess, Patlon III, | Abrasion-resistant | sportswear, sweaters |
Polystrand, Spectra, Synera, | Quick-drying | Home furnishings: carpet and carpet backing, |
Trace | Resistant to deterioration from chemicals, | slipcovers, upholstery |
mildew, perspiration, rot, and weather | 0ther: dye nets, filter fabrics, laundry and sand- | |
Sensitive to heat | bags, geotextiles, automotive interiors, | |
Soilresistant | cordage, doll hair, industrial sewing thread | |
Strong; very lightweight | ||
Excellent colorfastness | ||
Polyester | Strong | Apparel: blouses, shirts, career apparel, |
A.C.E., Ceylon, Comfort Fiber, | Resistant to stretching and shrinking | children’s wear, dresses, half hose, insulated |
Compet, Coolmax, | Resistant to most chemicals | garments, ties, lingerie and underwear, |
Corebond, Dacronfi, ES.P, | Quick-drying | permanent press garments, slacks, suits |
Fortel, Hollofi, Kodaire, | Crisp and resilient when wet or dry | Home furnishings: carpets, curtains, draperies, |
Kodel, Kod0fill, Kod0soff, | Wrinkle- and abrasion-resistant | sheets and pillow cases |
Pentron, Premafill Plurnp, | Retains heat-set pleats and creases | 0ther: fiberfill for various products, fire hose, |
Premafill Soft, KoSa, KoSa | Easy to wash | power belting, ropes and nets, tire cord, sail, |
Finesse, KoSa Micronesse, | V-belts | |
Universe | ||
PBI | Highly flame resistant | Suitable for high-performance protective |
PBI Logo | 0utstanding comfort factor combined with | apparelsuch as firemen’s turnout coats, |
thermaland chemicalstability | astronaut space suits and applications where | |
properties | fire resistance is important | |
Will not burn or melt | ||
Low shrinkage when exposed to flame | ||
Rayon | Highly absorbent | Apparel: blouses, coats, dresses, jackets, |
Beau-Grip, Fibro, Galaxy | Soft and comfortable | lingerie, linings, millinery, rainwear, slacks, |
Easy to dye | sports shirts, sportswear, suits, suits, ties, | |
Versatile | work clothes | |
Good drapability | Home furnishings: bedspreads, blankets, carpets, curtains, draperies, sheets, slipcovers, tablecloths, upholstery 0ther: industrialproducts, medical, surgical products, nonwoven products, tire cord | |
Spandex | Can be stretched 500% without breaking | Articles (where stretch is desired): athletic |
Lycra | Can be stretched repeatedly and returns to | apparel, bathing suits, delicate laces, |
originallength | foundation garments, golfjackets, ski pants, | |
Light-weight | slacks, support and surgical hose | |
Stronger and more durable than rubber | ||
Resistant to body oils | ||
Sulfar | High-performance fibers with excellent | Filter fabric for coal-fired boiler bag houses, |
Ryton | resistance to harsh chemicals and high | papermakers’ felts, electrical insulation, |
temperatures | electrolysis membranes, filter fabrics for | |
Excellent strength retention in adverse | liquid and gas filtration, high-performance | |
environments | composites, gaskets and packing | |
Flame retardant | ||
Nonconductive |
Cellulose is a cellulosic polymer identical to cotton, but with a much lower degree of polymerization. This results in a number of significant differences in the physical and chemical properties between the two polymers. Viscose (as generally with other regenerated cellulosic polymers) is a weaker fiber, with a lower abrasion resistance, lower heat resistance, lower wet strength and poorer heat conductivity than cotton. However, it is the cheapest artificial fiber, and is therefore used for dress fabrics, underwear and furnishings, often blended with cotton, nylon, polyester or wool. Non-woven products include bedding and personal hygiene products, where the moisture absorption is important. Commercial trade names include Rayonne, Cidena, Rhovalan, Torayon, IF80, Tenasco (higher tenacity viscose). Viloft (hollow viscose). Darelle (flame retardant viscose).
An example of viscose fiber is shown in Fig. 7.
Modal (polynosic) rayon Modal rayon fibers are obtained by a modified viscose manufacturing process: a very slow regeneration in the presence of dilute acid and a high concentration of zinc sulfate, accompanied by a very high degree of applied stretch. The highly oriented structure imparts a high degree of strength in both dry and wet states, lower extension at break and lower moisture regain. Zantrel is an example of commercial trade name.

Figure 7 Viscose rayon fiber (magnification 90 x).
Cuprammonium rayon Historically, cuprammo-nium rayon was the first commercially useful artificial fiber. Cellulose pulp is solubilized in an ammonia solution containing copper salt and caustic soda. The fiber has very similar physical and chemical properties to those of viscose (one minor difference is that the pore size of cupro fibers is larger than that of viscose, so that cupro fibers stain and dye more readily). However, the high cost of cupro production, involving the use of copper salts, resulted in cupro being superseded by viscose in the 1940s. In fact, cupro fiber is now virtually obsolete.
Lyocell Lyocell is a relatively new type of fiber which is defined as a cellulose fiber obtained by an organic solvent spinning process without the formation of a derivative. In this process, raw cellulose is directly dissolved in an amine oxide solvent. The solution is then filtered, and extruded into an aqueous bath of dilute amine oxide, and coagulated into fiber form. Although it is given a separate generic name, the Federal Trade Commission (US) classifies Lyocell as a subcategory under ‘Rayon’.
Lyocell fibers are soft, strong, absorbent, wrinkle resistant, biodegradable, and have excellent wet strength. Lyocell produces versatile fabric dyable to vibrant colors, with a variety of effects and textures which simulates silk, suede or leather touch. It is used for dresses, slacks, coats and jeans. Trade names include Lenzing Lyocell and Tencel.
Lyocell can be distinguished from other cellulosic fibers, including viscose and modal fibers, by a careful examination of their morphology and by accurate birefringence measurements.
Cellulose Ester Fibers (Cellulose Acetate and Cellulose Triacetate) Both acetate and triacetate are ester derivatives of the natural cellulose polymer, in which the hydroxyl groups have been acetylated to form the ester of acetic acid using acetic acid, acetic anhydride and sulfuric acid (as catalyst). The complete conversion of all (6) OH groups in glucose monomer into acetate groups (-OCOCH3) leads to triacetate (or primary cellulose acetate). The partial hydrolysis of the fully acetylated polymer, leaving 74-92% of the hydroxyl groups acetylated, leads to acetate (or secondary cellulose acetate).
In comparison to viscose, cellulose esters are weaker fibers, which become even weaker when wet. Acetate and triacetate materials distort or wrinkle easily. The moisture absorbencies of acetate and triacetate fibers are lower than that of viscose. Both fibers are thermoplastic, that is they may be permanently set or pleated by the application of heat.
Acetate and triacetate fibers are used in most fabric and garment end uses for their silk-like appearance, soft handle and easy dying. Their tenacities are adequate for dress wear, linings and furnishing fabrics, and they are often blended with cotton and synthetics. Trade names for acetate include Rhodia, Albene, Rhodalha and Seraceta. Trade names for triacetate include Rhonel and Tricel.
Examples of cellulose acetate fiber are shown in Figs 8 and 9.
Regenerated protein fibers Regenerated protein fibers are manufactured by extruding an alkaline solution of protein (casein, peanuts, soya, wool, etc.) followed by coagulation in acid. Further treatment with formaldehyde improves resistance to alkalis. The surface of the fiber is smooth and the cross-section is almost round. Regenerated protein fibers may be distinguished from silk by their insolubility in cold concentrated hydrochloric acid in which silk dissolves. Regenerated protein fibers are usually incorporated into blends with other fibers such as cotton and wool.

Figure 8 Cellulose acetate fiber (magnification 90 x).

Figure 9 Cellulose triacetate fiber (magnification 90 x).
Alginate fibers Alginate fibers are prepared by spinning an aqueous solution of sodium alginate (polymers of mannuronic acid and guluronic acid) extracted from seaweed. The solution is coagulated in a bath of calcium chloride as calcium alginate (precipitate). The fiber is nonflammable owing to its high metal content, and it is soluble in alkaline solution. Alginate fibers may be used in similar end uses as water-soluble polyvinyl alcohol (PVA) (see below). The principal application is, however, in surgical end uses, where the water-soluble form of sodium alginate is readily absorbed in the bloodstream. The appearance of alginate fibers is similar to those of viscose (longitudinal striations, irregular cross-section). Alginate fibers are characterized by their high ash content, and their solubility in carbonate solution.
An example of viscose fiber is shown in Fig. 7.
Modal (polynosic) rayon Modal rayon fibers are obtained by a modified viscose manufacturing process: a very slow regeneration in the presence of dilute acid and a high concentration of zinc sulfate, accompanied by a very high degree of applied stretch. The highly oriented structure imparts a high degree of strength in both dry and wet states, lower extension at break and lower moisture regain. Zantrel is an example of commercial trade name.
Figure 7 Viscose rayon fiber (magnification 90 x).
Cuprammonium rayon Historically, cuprammo-nium rayon was the first commercially useful artificial fiber. Cellulose pulp is solubilized in an ammonia solution containing copper salt and caustic soda. The fiber has very similar physical and chemical properties to those of viscose (one minor difference is that the pore size of cupro fibers is larger than that of viscose, so that cupro fibers stain and dye more readily). However, the high cost of cupro production, involving the use of copper salts, resulted in cupro being superseded by viscose in the 1940s. In fact, cupro fiber is now virtually obsolete.
Lyocell Lyocell is a relatively new type of fiber which is defined as a cellulose fiber obtained by an organic solvent spinning process without the formation of a derivative. In this process, raw cellulose is directly dissolved in an amine oxide solvent. The solution is then filtered, and extruded into an aqueous bath of dilute amine oxide, and coagulated into fiber form. Although it is given a separate generic name, the Federal Trade Commission (US) classifies Lyocell as a subcategory under ‘Rayon’.
Lyocell fibers are soft, strong, absorbent, wrinkle resistant, biodegradable, and have excellent wet strength. Lyocell produces versatile fabric dyable to vibrant colors, with a variety of effects and textures which simulates silk, suede or leather touch. It is used for dresses, slacks, coats and jeans. Trade names include Lenzing Lyocell and Tencel.
Lyocell can be distinguished from other cellulosic fibers, including viscose and modal fibers, by a careful examination of their morphology and by accurate birefringence measurements.
Cellulose Ester Fibers (Cellulose Acetate and Cellulose Triacetate) Both acetate and triacetate are ester derivatives of the natural cellulose polymer, in which the hydroxyl groups have been acetylated to form the ester of acetic acid using acetic acid, acetic anhydride and sulfuric acid (as catalyst). The complete conversion of all (6) OH groups in glucose monomer into acetate groups (-OCOCH3) leads to triacetate (or primary cellulose acetate). The partial hydrolysis of the fully acetylated polymer, leaving 74-92% of the hydroxyl groups acetylated, leads to acetate (or secondary cellulose acetate).
In comparison to viscose, cellulose esters are weaker fibers, which become even weaker when wet. Acetate and triacetate materials distort or wrinkle easily. The moisture absorbencies of acetate and triacetate fibers are lower than that of viscose. Both fibers are thermoplastic, that is they may be permanently set or pleated by the application of heat.
Acetate and triacetate fibers are used in most fabric and garment end uses for their silk-like appearance, soft handle and easy dying. Their tenacities are adequate for dress wear, linings and furnishing fabrics, and they are often blended with cotton and synthetics. Trade names for acetate include Rhodia, Albene, Rhodalha and Seraceta. Trade names for triacetate include Rhonel and Tricel.
Examples of cellulose acetate fiber are shown in Figs 8 and 9.
Regenerated protein fibers Regenerated protein fibers are manufactured by extruding an alkaline solution of protein (casein, peanuts, soya, wool, etc.) followed by coagulation in acid. Further treatment with formaldehyde improves resistance to alkalis. The surface of the fiber is smooth and the cross-section is almost round. Regenerated protein fibers may be distinguished from silk by their insolubility in cold concentrated hydrochloric acid in which silk dissolves. Regenerated protein fibers are usually incorporated into blends with other fibers such as cotton and wool.
Figure 8 Cellulose acetate fiber (magnification 90 x).
Figure 9 Cellulose triacetate fiber (magnification 90 x).
Alginate fibers Alginate fibers are prepared by spinning an aqueous solution of sodium alginate (polymers of mannuronic acid and guluronic acid) extracted from seaweed. The solution is coagulated in a bath of calcium chloride as calcium alginate (precipitate). The fiber is nonflammable owing to its high metal content, and it is soluble in alkaline solution. Alginate fibers may be used in similar end uses as water-soluble polyvinyl alcohol (PVA) (see below). The principal application is, however, in surgical end uses, where the water-soluble form of sodium alginate is readily absorbed in the bloodstream. The appearance of alginate fibers is similar to those of viscose (longitudinal striations, irregular cross-section). Alginate fibers are characterized by their high ash content, and their solubility in carbonate solution.
Synthetic fibers
All synthetic fibers are organic polymeric fibers manufactured by chemical synthesis. The polymer formation is obtained by condensation (loss of water) or addition (no loss), the final product being respectively referred to as condensation and addition polymers. Examples of condensation polymers include polya-mide and aramids, polyesters and polyurethanes, and examples of addition polymers include polyolefins and polyvinyl derivatives (cf. below).
The first synthetic fiber, nylon, was developed by Carothers in 1927, but it was only after World War II that mass production started. Nowadays, synthetic fibers are necessary to our daily activity, used alone or blended with natural fibers. They represent an important part of the world production of textile materials, and are a priori frequently encountered in criminal investigation. Most common synthetic fibers are described below and a few examples are shown in Figs 10-12.
Polyamides (nylon, qiana and aramid) Polyamides are organic polymer fibers which contain an amide functionality (-CONH-) within the repeating unit. The polymer may be aliphatic (nylon), alicyclic (quiana) or aromatic (aramid).
Nylon Aliphatic polyamides are defined according to the number of carbon atoms in the repeating unit. Nylon 6.6 and nylon 6 are the most widely manufactured polyamides (Fig. 13).

Figure 10 Nylon fiber (magnification 90 x).

Figure 11 Polyester fiber (magnification 90x ).

Figure 12 Acrylic (0rlon) fiber (magnification 9 x).

Figure 13 Two examples of Nylon fibers.
• Nylon 6.6 is the condensation product of hexam-ethylene diamine and adipic acid. Due to the high degree of crystallinity, nylon 6.6 is the most abrasion resistant of all common textile fibers (four to five times better than wool), with a good tensile strength (even wet) and an excellent elastic recovery. Nylon 6.6 is relatively flammable, chemically stable, but unstable to sunlight. The melting point is in the range of 250-260°C. Nylon 6.6 is commonly used for ropes and cordages, carpets, fishing nets, brushes (e.g. toothbrushes) and common garments (under- and outer garments, often blended with cotton). Trade names of nylon 6.6 include Blue C, ICI-nylon, Perlon T, Ultron, Nylfrance, Obtel, Oranyl, Amilan.
• Nylon 6 is the condensation product of 6-amino-hexanoic acid. Nylon 6 is easier to dye than nylon 6.6, and is therefore cheaper. The low melting point (approx. 215°C) constitutes a drawback because the garments are difficult to iron. The other properties of nylon 6 are similar to those of nylon 6.6. Nylon 6 is used as tire reinforcement, in carpets, and other similar applications to those of nylon 6.6. Trade names of nylon 6 include Perlon, Celon, Montefiber, Enkalon, Dederon, Grilon, Lilion, Forlion, Perlofil, Dayan.
Other aliphatic polyamides that have been commercialized include nylon 4.6, nylon 6.10, nylon 7 and nylon 11 (Rilsan).Some of these fibers have been developed for their exceptional resistance to abrasion and thermal degradation in engineering applications.
New nylon 6-based block copolymer fibers have been developed recently. These fibers have the strength, durability and thermoplasticity of nylon but with a moisture absorption which is similar to that of cotton. Infrared spectrometry is required to distinguish nylon 6-based block copolymers from normal nylon 6.
Quiana Qiana (or PACM-12): is a polyamide containing an alicyclic group and a long 12-membered carbon chain: [-HN-C6H8-CH2-C6H8-NHCO-(CH2)10-CO]. This is a fashion fabric known for its silk-like handle and high moisture regain.
Aramids: There are aromatic polyamides defined as having at least 85% of their amide linkage attached directly to two aromatic rings. Nomex and Kevlar are the most commonly encountered aramids (Figs 14 and 15).
Aramids fibers have exceptional mechanical, chemical and heat resistance. Nomex is inherently flame retardant and kevlar is five times stronger than steel and more than 10 times stronger than aluminum. However, their expense limits application to high-performance products, for example sporting goods, high performance tires and the aerospace industry.
Polyesters Polyesters are polymers containing at least 85% (mass) of the ester obtained by the condensation of a diol and a dicarboxylic acid. The most common types of polyesters are polyethylene terephthalate (PET, trade names: Terilene, Dacron, Trevira, Tergal)(Fig. 16) and poly-1,4-cyclohexylene-dimethylene terephthalate (PCDT, trade name: Kodel), (Fig. 17).
PET fibers have a good tensile strength, and are resistant to chemicals, biological agents and abrasion. They are more flammable than nylon, but more resistant to sunlight. The melting point is around 250°C. PCDT fibers have a good elasticity and are more heat resistant than PET fibers (melting point around 290°C). Their flammability is negligible. Otherwise, their properties are similar to those of PET. Polyesters are used in numerous applications, for example garments (often blended with wool or cotton), linen, ropes, tire reinforcement.
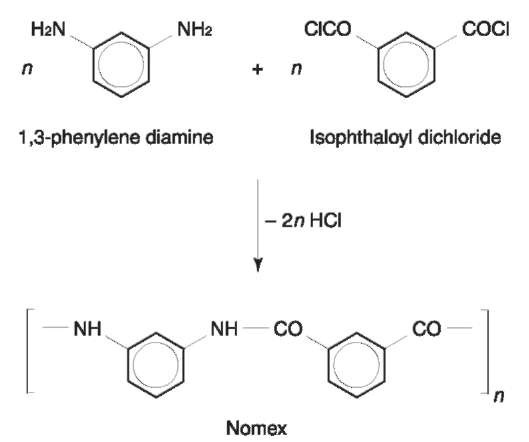
Figure 14 Nomex: benzene rings are mefa-substituted.

Figure 15 Kevlar: benzene rings are para-substituted.

Figure 17 PCDT fibers.
Polyurethanes Polyurethane elastomeric fibers (‘elastane’) are defined as containing at least 85% by mass of recurrent aliphatic groups joined by urethane linkages [-O-CO-NH-]. Polyurethanes are very complex polymers combining a flexible segment, which provides the high degree of stretch and rapid recovery of an elastomer, with a rigid segment that confers the necessary strength of a fiber (Fig. 18).
Polyurethanes fibers have distinctive highly extensible ‘snap-back’ properties (500-600% elongation). As a result they are often incorporated into fabrics for the purpose of comfort and fit (swimwear, active wear, undergarments, etc.). Trade names include Lycra, Vyrene, Dorian, Dorlastan, Lastex S, Rhodas-tic, Sarlan, Spandelle.
Polyolefins Polyolefin fibers are defined as containing at least 85% by mass of ethylene, propylene or other olefin units (amorphous olefins excepted). Polyethylene and polypropylene are the two most important types of polyolefins.

Figure 18 Formation of polyurethanes.
Polyethylene Free radical polymerization under conditions of high temperature and pressure, leads to the formation of low-density polyethylene (LDPE) unsuitable as fibrous material. The use of a special catalyst system allows the formation of a highly crystalline polymer network known as high-density polyethylene (HDPE) (Fig. 19). Polyethylene fibers have good chemical and biological stability. The melting point is low (around 120°C). They are relatively cheap, light and their flammability is in the medium range (they burn slowly). They have a zero moisture regain. They are sensitive to sunlight degradation. As a result, they have few textile applications. They are used for chemical filtration, car upholstery, medical products and next-to-skin active wear. Trade names include Courlene, Drylene, Polythene and Marlex.
Polypropylene The manufacture of polypropylene fibers (Fig. 20) is much simpler and cheaper than other synthetic fibers such as nylon or polyester. Polypropylene fibers are resistant to solvents and other chemicals, to bacteriological growth and to abrasion. The melting point is relatively low (but higher than that of polyethylene, around 165°C). These fibers are relatively light and have a good tensile strength. They have a highly crystalline and hydrophobic nature. They are therefore easily washed and dryed. They constitute an excellent thermal insulation material. The other properties of polypropylene fibers are similar to those of polyethylene. Polypropylene fibers are used as alternatives to natural fibers such as sisal or jute. They can be incorporated in the manufacture of ropes, fishing nets, carpets, furniture fabrics, protective garments, synthetic paper, etc. Trade names include Aberclare, Deltafil, Fibrite, Gymlene, Hercu-lon, Meraklon, Neofil, Polycrest, Pylen, Reevon, Spunstron and Tritor.

Figure 20 Polypropylene fibers.
Polyacrylonitrile (acrylics and modacrylics) Poly-acrylonitrile fibers are composed of repeating acrylo-nitrile units [-CH2CHCN-]. There are two groups of polyacrylonitrile fibers: acrylics and modacrylics.
Acrylics These fibers have at least 85% (mass) of acrylonitrile units (Fig. 21). Examples of the most common compositions for acrylic fibers are: acrylo-nitrile/methyl acrylate, acrylonitrile/vinyl acetate, or acrylonitrile/methyl methacrylate. The purpose of the comonomers is to open the polymeric structure and/or incorporate anionic and cationic groups in the polymer system in order to facilitate the dying process.
Acrylic fibers have a low moisture regain, and a moderate tensile strength compared to nylon and polyester. The resistance to abrasion is moderate (poorer than that of nylon). These fibers are insoluble in most organic solvents. The resistance to poor weather conditions and sunlight is excellent. However, acrylic fibers are very heat sensitive and readily flammable on close approach to a flame. Acrylic fibers are very versatile and have numerous applications, such as outdoors furniture, tents, curtains, carpets, knitted outerwear, usually blended with other fibers to impart flame retardancy. Trade names include Acrilan, Courtelle, Creslan, Crylor, Dralon, Orlon, Sayelle and Zefran.
Modacrylics These fibers are composed of at least 35%, but no more than 85%, of acrylonitrile units. Common trade names include Crylor, Dynel, Kanecaron, SEF modacrylic, Teklan, Verel (Fig. 22).

Figure 21 Acrylic fibers.

Figure 22 Modacrylic fibers.
Chlorine-containing modacrylics (e.g. Dynel) do not support combustion and are considered to be flame resistant, i.e. the flame is extinguished rather than being propagated. However, chlorine-containing modacrylics have lower heat resistance and shrink markedly in boiling water. Modacrylics have similar application to those of acrylics. They are also usually blended with other fibers to impart flame retardancy in apparel and furnishings.
Chlorofibers Chlorofibers are manufactured from either polyvinyl chloride (PVC) or polyvinylidene chloride (PVDC).
Polyvinyl chloride (PVC) These fibers are composed of at least 85% (mass) of vinyl chloride repeating units (Fig. 23). PVC fibers have medium tenacity, high elongation, and high degree of shrinkage (up to 40%) at relatively low temperature (100°C). They have virtually zero moisture regain and excellent resistance to corrosive chemicals. PVC fibers are also photostable and intrinsically nonflammable. Coloration is however a problem, and they are soluble in chlorinated hydrocarbons and aromatic solvents, rendering them unsuitable for dry cleaning. End use applications are therefore filter fabrics, woven fabrics such as drapery, blankets and underwear, ropes, fishing nets, etc. Trade names include Clevyl T, Dynel, Kurekalon, Fibravyl, Retractyl, Rhovyl, Thermovyl.

Figure 23 Polyvinyl chloride fibers.
Polyvinylidene chloride (PVDC) These fibers are composed of at least 80% (mass) of vinylidene chloride as repeating units (Fig. 24). PVDC fibers are relatively cheap and their resistance to chemicals is better than that of nylon. They are nonflammable, but shrink at 220°C. They are relatively heavy and extremely water resistant, and have good tenacity. PVDC fibers are used in furniture fabrics, car upholstery (as leather substitute), carpets, etc. The most common trade name for PVDC fibers is Saran.
Fluorofibers Fluorofibers are composed of fluorocarbon as repeating units. The most common fluorofiber is polytetrafluoroethylene (PTFE) known under the trade name of Teflon (Fig. 25). The chain of PTFE forms a highly organized close-packed arrangement. As a result, the fibers have the highest density of any fiber of organic origin. The inertness of the fluorine atoms, combined with the packing symmetry offers a very effective barrier to corrosive chemicals,giving a fiber with outstanding resistance toward heat (stable up to 250°C, nonflammable), chemicals, and solvents. Other properties include a good resistance to abrasion and zero moisture absorbency. PTFE fibers are produced in small quantities for highly specialized end uses, for example filtration of liquids and gases under high temperature and/or corrosive conditions, protective garments. Fluorofibers are also manufactured in Japan under the trade names of Polyflon or Toyoflon.

Figure 24 Polyvinylidene chloride fibers.

Figure 25 Polytetrafluoroethylene fibers.
Vinylals Vinylals are polyvinyl alcohol chains (PVA) defined as fibers containing at least 50% (mass) of vinyl alcohol and at least 85% (mass) of acetals and vinyl alcohol units. They are produced by the polymerization of the stable vinyl actetate monomer, where subsequent hydrolysis of polyvinyl acetate yields the polyvinyl alcohol polymer (Fig. 26). PVA fibers are normally water soluble. However, subsequent acetylation of the OH groups or an after-treatment with formaldehyde renders PVA fibers resistant to boiling water. PVA fibers have generally poor elastic recovery and wrinkle easily. They do not burn easily and have a good chemical and biological stability. PVA fibers exist in a wide range of tenacity. The melting point is around 230°C. PVA fibers are popular in Japan (15% of the total production of fibers) for many textile apparel uses (e.g. kimonos) and industrial applications. They are a good biological resistant substitute for cellulose fibers in fishing nets, ropes, packaging materials, etc. Common trade names include Cremona, Kuralon, Mewlon and Vinylon.
The first synthetic fiber, nylon, was developed by Carothers in 1927, but it was only after World War II that mass production started. Nowadays, synthetic fibers are necessary to our daily activity, used alone or blended with natural fibers. They represent an important part of the world production of textile materials, and are a priori frequently encountered in criminal investigation. Most common synthetic fibers are described below and a few examples are shown in Figs 10-12.
Polyamides (nylon, qiana and aramid) Polyamides are organic polymer fibers which contain an amide functionality (-CONH-) within the repeating unit. The polymer may be aliphatic (nylon), alicyclic (quiana) or aromatic (aramid).
Nylon Aliphatic polyamides are defined according to the number of carbon atoms in the repeating unit. Nylon 6.6 and nylon 6 are the most widely manufactured polyamides (Fig. 13).
Figure 10 Nylon fiber (magnification 90 x).
Figure 11 Polyester fiber (magnification 90x ).
Figure 12 Acrylic (0rlon) fiber (magnification 9 x).
Figure 13 Two examples of Nylon fibers.
• Nylon 6.6 is the condensation product of hexam-ethylene diamine and adipic acid. Due to the high degree of crystallinity, nylon 6.6 is the most abrasion resistant of all common textile fibers (four to five times better than wool), with a good tensile strength (even wet) and an excellent elastic recovery. Nylon 6.6 is relatively flammable, chemically stable, but unstable to sunlight. The melting point is in the range of 250-260°C. Nylon 6.6 is commonly used for ropes and cordages, carpets, fishing nets, brushes (e.g. toothbrushes) and common garments (under- and outer garments, often blended with cotton). Trade names of nylon 6.6 include Blue C, ICI-nylon, Perlon T, Ultron, Nylfrance, Obtel, Oranyl, Amilan.
• Nylon 6 is the condensation product of 6-amino-hexanoic acid. Nylon 6 is easier to dye than nylon 6.6, and is therefore cheaper. The low melting point (approx. 215°C) constitutes a drawback because the garments are difficult to iron. The other properties of nylon 6 are similar to those of nylon 6.6. Nylon 6 is used as tire reinforcement, in carpets, and other similar applications to those of nylon 6.6. Trade names of nylon 6 include Perlon, Celon, Montefiber, Enkalon, Dederon, Grilon, Lilion, Forlion, Perlofil, Dayan.
Other aliphatic polyamides that have been commercialized include nylon 4.6, nylon 6.10, nylon 7 and nylon 11 (Rilsan).Some of these fibers have been developed for their exceptional resistance to abrasion and thermal degradation in engineering applications.
New nylon 6-based block copolymer fibers have been developed recently. These fibers have the strength, durability and thermoplasticity of nylon but with a moisture absorption which is similar to that of cotton. Infrared spectrometry is required to distinguish nylon 6-based block copolymers from normal nylon 6.
Quiana Qiana (or PACM-12): is a polyamide containing an alicyclic group and a long 12-membered carbon chain: [-HN-C6H8-CH2-C6H8-NHCO-(CH2)10-CO]. This is a fashion fabric known for its silk-like handle and high moisture regain.
Aramids: There are aromatic polyamides defined as having at least 85% of their amide linkage attached directly to two aromatic rings. Nomex and Kevlar are the most commonly encountered aramids (Figs 14 and 15).
Aramids fibers have exceptional mechanical, chemical and heat resistance. Nomex is inherently flame retardant and kevlar is five times stronger than steel and more than 10 times stronger than aluminum. However, their expense limits application to high-performance products, for example sporting goods, high performance tires and the aerospace industry.
Polyesters Polyesters are polymers containing at least 85% (mass) of the ester obtained by the condensation of a diol and a dicarboxylic acid. The most common types of polyesters are polyethylene terephthalate (PET, trade names: Terilene, Dacron, Trevira, Tergal)(Fig. 16) and poly-1,4-cyclohexylene-dimethylene terephthalate (PCDT, trade name: Kodel), (Fig. 17).
PET fibers have a good tensile strength, and are resistant to chemicals, biological agents and abrasion. They are more flammable than nylon, but more resistant to sunlight. The melting point is around 250°C. PCDT fibers have a good elasticity and are more heat resistant than PET fibers (melting point around 290°C). Their flammability is negligible. Otherwise, their properties are similar to those of PET. Polyesters are used in numerous applications, for example garments (often blended with wool or cotton), linen, ropes, tire reinforcement.
Figure 14 Nomex: benzene rings are mefa-substituted.
Figure 15 Kevlar: benzene rings are para-substituted.
Figure 17 PCDT fibers.
Polyurethanes Polyurethane elastomeric fibers (‘elastane’) are defined as containing at least 85% by mass of recurrent aliphatic groups joined by urethane linkages [-O-CO-NH-]. Polyurethanes are very complex polymers combining a flexible segment, which provides the high degree of stretch and rapid recovery of an elastomer, with a rigid segment that confers the necessary strength of a fiber (Fig. 18).
Polyurethanes fibers have distinctive highly extensible ‘snap-back’ properties (500-600% elongation). As a result they are often incorporated into fabrics for the purpose of comfort and fit (swimwear, active wear, undergarments, etc.). Trade names include Lycra, Vyrene, Dorian, Dorlastan, Lastex S, Rhodas-tic, Sarlan, Spandelle.
Polyolefins Polyolefin fibers are defined as containing at least 85% by mass of ethylene, propylene or other olefin units (amorphous olefins excepted). Polyethylene and polypropylene are the two most important types of polyolefins.
Figure 18 Formation of polyurethanes.
Polyethylene Free radical polymerization under conditions of high temperature and pressure, leads to the formation of low-density polyethylene (LDPE) unsuitable as fibrous material. The use of a special catalyst system allows the formation of a highly crystalline polymer network known as high-density polyethylene (HDPE) (Fig. 19). Polyethylene fibers have good chemical and biological stability. The melting point is low (around 120°C). They are relatively cheap, light and their flammability is in the medium range (they burn slowly). They have a zero moisture regain. They are sensitive to sunlight degradation. As a result, they have few textile applications. They are used for chemical filtration, car upholstery, medical products and next-to-skin active wear. Trade names include Courlene, Drylene, Polythene and Marlex.
Polypropylene The manufacture of polypropylene fibers (Fig. 20) is much simpler and cheaper than other synthetic fibers such as nylon or polyester. Polypropylene fibers are resistant to solvents and other chemicals, to bacteriological growth and to abrasion. The melting point is relatively low (but higher than that of polyethylene, around 165°C). These fibers are relatively light and have a good tensile strength. They have a highly crystalline and hydrophobic nature. They are therefore easily washed and dryed. They constitute an excellent thermal insulation material. The other properties of polypropylene fibers are similar to those of polyethylene. Polypropylene fibers are used as alternatives to natural fibers such as sisal or jute. They can be incorporated in the manufacture of ropes, fishing nets, carpets, furniture fabrics, protective garments, synthetic paper, etc. Trade names include Aberclare, Deltafil, Fibrite, Gymlene, Hercu-lon, Meraklon, Neofil, Polycrest, Pylen, Reevon, Spunstron and Tritor.
Figure 20 Polypropylene fibers.
Polyacrylonitrile (acrylics and modacrylics) Poly-acrylonitrile fibers are composed of repeating acrylo-nitrile units [-CH2CHCN-]. There are two groups of polyacrylonitrile fibers: acrylics and modacrylics.
Acrylics These fibers have at least 85% (mass) of acrylonitrile units (Fig. 21). Examples of the most common compositions for acrylic fibers are: acrylo-nitrile/methyl acrylate, acrylonitrile/vinyl acetate, or acrylonitrile/methyl methacrylate. The purpose of the comonomers is to open the polymeric structure and/or incorporate anionic and cationic groups in the polymer system in order to facilitate the dying process.
Acrylic fibers have a low moisture regain, and a moderate tensile strength compared to nylon and polyester. The resistance to abrasion is moderate (poorer than that of nylon). These fibers are insoluble in most organic solvents. The resistance to poor weather conditions and sunlight is excellent. However, acrylic fibers are very heat sensitive and readily flammable on close approach to a flame. Acrylic fibers are very versatile and have numerous applications, such as outdoors furniture, tents, curtains, carpets, knitted outerwear, usually blended with other fibers to impart flame retardancy. Trade names include Acrilan, Courtelle, Creslan, Crylor, Dralon, Orlon, Sayelle and Zefran.
Modacrylics These fibers are composed of at least 35%, but no more than 85%, of acrylonitrile units. Common trade names include Crylor, Dynel, Kanecaron, SEF modacrylic, Teklan, Verel (Fig. 22).
Figure 21 Acrylic fibers.
Figure 22 Modacrylic fibers.
Chlorine-containing modacrylics (e.g. Dynel) do not support combustion and are considered to be flame resistant, i.e. the flame is extinguished rather than being propagated. However, chlorine-containing modacrylics have lower heat resistance and shrink markedly in boiling water. Modacrylics have similar application to those of acrylics. They are also usually blended with other fibers to impart flame retardancy in apparel and furnishings.
Chlorofibers Chlorofibers are manufactured from either polyvinyl chloride (PVC) or polyvinylidene chloride (PVDC).
Polyvinyl chloride (PVC) These fibers are composed of at least 85% (mass) of vinyl chloride repeating units (Fig. 23). PVC fibers have medium tenacity, high elongation, and high degree of shrinkage (up to 40%) at relatively low temperature (100°C). They have virtually zero moisture regain and excellent resistance to corrosive chemicals. PVC fibers are also photostable and intrinsically nonflammable. Coloration is however a problem, and they are soluble in chlorinated hydrocarbons and aromatic solvents, rendering them unsuitable for dry cleaning. End use applications are therefore filter fabrics, woven fabrics such as drapery, blankets and underwear, ropes, fishing nets, etc. Trade names include Clevyl T, Dynel, Kurekalon, Fibravyl, Retractyl, Rhovyl, Thermovyl.
Figure 23 Polyvinyl chloride fibers.
Polyvinylidene chloride (PVDC) These fibers are composed of at least 80% (mass) of vinylidene chloride as repeating units (Fig. 24). PVDC fibers are relatively cheap and their resistance to chemicals is better than that of nylon. They are nonflammable, but shrink at 220°C. They are relatively heavy and extremely water resistant, and have good tenacity. PVDC fibers are used in furniture fabrics, car upholstery (as leather substitute), carpets, etc. The most common trade name for PVDC fibers is Saran.
Fluorofibers Fluorofibers are composed of fluorocarbon as repeating units. The most common fluorofiber is polytetrafluoroethylene (PTFE) known under the trade name of Teflon (Fig. 25). The chain of PTFE forms a highly organized close-packed arrangement. As a result, the fibers have the highest density of any fiber of organic origin. The inertness of the fluorine atoms, combined with the packing symmetry offers a very effective barrier to corrosive chemicals,giving a fiber with outstanding resistance toward heat (stable up to 250°C, nonflammable), chemicals, and solvents. Other properties include a good resistance to abrasion and zero moisture absorbency. PTFE fibers are produced in small quantities for highly specialized end uses, for example filtration of liquids and gases under high temperature and/or corrosive conditions, protective garments. Fluorofibers are also manufactured in Japan under the trade names of Polyflon or Toyoflon.
Figure 24 Polyvinylidene chloride fibers.
Figure 25 Polytetrafluoroethylene fibers.
Vinylals Vinylals are polyvinyl alcohol chains (PVA) defined as fibers containing at least 50% (mass) of vinyl alcohol and at least 85% (mass) of acetals and vinyl alcohol units. They are produced by the polymerization of the stable vinyl actetate monomer, where subsequent hydrolysis of polyvinyl acetate yields the polyvinyl alcohol polymer (Fig. 26). PVA fibers are normally water soluble. However, subsequent acetylation of the OH groups or an after-treatment with formaldehyde renders PVA fibers resistant to boiling water. PVA fibers have generally poor elastic recovery and wrinkle easily. They do not burn easily and have a good chemical and biological stability. PVA fibers exist in a wide range of tenacity. The melting point is around 230°C. PVA fibers are popular in Japan (15% of the total production of fibers) for many textile apparel uses (e.g. kimonos) and industrial applications. They are a good biological resistant substitute for cellulose fibers in fishing nets, ropes, packaging materials, etc. Common trade names include Cremona, Kuralon, Mewlon and Vinylon.
Other artificial fibers
Carbon fibers Carbon fibers are prepared from existing artificial fibers, most commonly polyacrylonitrile. Manufacture involves a three-stage heating process during which the fiber is pyrolysed and carbonized leaving a pure carbon fiber. Carbon fibers are black and lustrous, and are very resistant to heat, although they tend to oxidize in air at 450°C. The outstanding performance of carbon fibers relates to their stiffness/weight ratio. Carbon complements Kevlar in performance. These fibers are used in the aerospace industry and sporting goods, where stiffness and light weight are essential criteria (overriding the high cost of production).

Figure 26 Polyvinyl alcohol fibers.
Glass fibers Glass fibers are manufactured in continuous form by mechanically drawing a molten stream of glass vertically downwards at high speed. Filament diameters are in the range 3-16 um, and multiple filaments (400-800) are brought together in a strand and processed into yarn, roving, woven, or chopped strand mats. These fibers possess a very high tensile strength, and a good temperature and chemical resistance. They are used for the reinforcement of plastics (boat building, pipes and tanks, etc.) and as filters. Trade names include Vetrotex, Fiberglas.
Ceramic fibers Ceramic fibers are a range of inorganic fibers specifically developed for their high temperature resistance.They generally contain either silica or alumina, or proportions of both. Other inorganic fibers also include silicon carbide and boron fibers. These fibers may be spun at very high speed from molten material and are as fine as glass fibers. Fabric applications include hot flue gas filtration, high efficiency air filtration in hospitals, etc., sterilizing filters in the preparation of beverages, thermal and acoustic insulation. Polybenzimidazole (PBI), phenolic (novoloid) and polyphenylene sulfide (PPS) are other inherently flame-retardant fibers which are suitable for protective clothing.
Metallized fibers These fibers are composed of gold, silver, stainless steel, brass containing nickel, aluminum, etc. Polyester films may be coated with a thin layer of vaporized metal (usually aluminum). The opposite is also possible; the two sides of an aluminum foil may be coated with a thermoplastic material. In both cases, the film is subsequently slit into 0.25-1.0 mm wide ribbons. These fibers have a very smooth surface and are usually used for textile decoration (e.g. Lurex).
Microfibers Microfibers are extremely fine fibers (< 7 um) developed in Japan in the mid-1970s as substitutes for silk.However they only appeared on the occidental market in the end of the 1980s. Micro-fibers are most often polyesters, although polya-mides, acrylics and viscose microfibers are also manufactured. The textile fabrics containing micro-fibers are silk-like, lighter and more resistant than traditional fabrics. These fibers are expensive due to the slow manufacture process. Typical applications of microfibers are ‘breathing’ sport garments which are permeable for water vapour, but constitute an efficient barrier for liquid water. Trade names include Mitrelle, Setila, Finesse. It should be noticed that their fine diameter presents a real analytical problem for the forensic fiber examiner.
BicomponentFibers Bicomponent fibers are composed of two different components, which can be two different polymers (two different comonomers) or two similar polymers containing different proportions of the same comonomer. The two different components can be assembled in two ways, either side-by-side, or one polymer embedded in the other. Bicomponent fibers are generally acrylics. Trade names include Acrilan B57 and Acrilan B94, Cash-milon, Creslan 68, Dralon K, Monsanto X-24, Orlon 21 and Orlon 78, Velicren.
Figure 26 Polyvinyl alcohol fibers.
Glass fibers Glass fibers are manufactured in continuous form by mechanically drawing a molten stream of glass vertically downwards at high speed. Filament diameters are in the range 3-16 um, and multiple filaments (400-800) are brought together in a strand and processed into yarn, roving, woven, or chopped strand mats. These fibers possess a very high tensile strength, and a good temperature and chemical resistance. They are used for the reinforcement of plastics (boat building, pipes and tanks, etc.) and as filters. Trade names include Vetrotex, Fiberglas.
Ceramic fibers Ceramic fibers are a range of inorganic fibers specifically developed for their high temperature resistance.They generally contain either silica or alumina, or proportions of both. Other inorganic fibers also include silicon carbide and boron fibers. These fibers may be spun at very high speed from molten material and are as fine as glass fibers. Fabric applications include hot flue gas filtration, high efficiency air filtration in hospitals, etc., sterilizing filters in the preparation of beverages, thermal and acoustic insulation. Polybenzimidazole (PBI), phenolic (novoloid) and polyphenylene sulfide (PPS) are other inherently flame-retardant fibers which are suitable for protective clothing.
Metallized fibers These fibers are composed of gold, silver, stainless steel, brass containing nickel, aluminum, etc. Polyester films may be coated with a thin layer of vaporized metal (usually aluminum). The opposite is also possible; the two sides of an aluminum foil may be coated with a thermoplastic material. In both cases, the film is subsequently slit into 0.25-1.0 mm wide ribbons. These fibers have a very smooth surface and are usually used for textile decoration (e.g. Lurex).
Microfibers Microfibers are extremely fine fibers (< 7 um) developed in Japan in the mid-1970s as substitutes for silk.However they only appeared on the occidental market in the end of the 1980s. Micro-fibers are most often polyesters, although polya-mides, acrylics and viscose microfibers are also manufactured. The textile fabrics containing micro-fibers are silk-like, lighter and more resistant than traditional fabrics. These fibers are expensive due to the slow manufacture process. Typical applications of microfibers are ‘breathing’ sport garments which are permeable for water vapour, but constitute an efficient barrier for liquid water. Trade names include Mitrelle, Setila, Finesse. It should be noticed that their fine diameter presents a real analytical problem for the forensic fiber examiner.
BicomponentFibers Bicomponent fibers are composed of two different components, which can be two different polymers (two different comonomers) or two similar polymers containing different proportions of the same comonomer. The two different components can be assembled in two ways, either side-by-side, or one polymer embedded in the other. Bicomponent fibers are generally acrylics. Trade names include Acrilan B57 and Acrilan B94, Cash-milon, Creslan 68, Dralon K, Monsanto X-24, Orlon 21 and Orlon 78, Velicren.
Conclusions
Textile fibers occur as a multitude of different possible types. The most common types encountered in a forensic context vary according to different climatic and socioeconomic environments, and also depend on a multitude of factors related to fiber transfer and persistence. However, cotton, wool, regenerated cellulose, polyesters, polyacrylonitrile and polyamide fibers are those most likely to be found in routine cases.
With current analytical techniques the forensic scientist is able to identify the generic class and subclass with a great degree of accuracy. This identification step is crucial in a forensic comparison and requires a great deal of experience and access to thorough reference information (certified samples, relevant atlas, manufacture data, etc.).
The challenge for the forensic scientist in a dynamic environment is to keep the data on the different products, manufacture changes and on how best to discriminate subclasses within a generic type up to date.
With current analytical techniques the forensic scientist is able to identify the generic class and subclass with a great degree of accuracy. This identification step is crucial in a forensic comparison and requires a great deal of experience and access to thorough reference information (certified samples, relevant atlas, manufacture data, etc.).
The challenge for the forensic scientist in a dynamic environment is to keep the data on the different products, manufacture changes and on how best to discriminate subclasses within a generic type up to date.
No comments:
Post a Comment